Scientists have been experimenting with alternative fuel sources for vehicles for decades. While drivers likely won’t be using food scraps to fuel their trucks anytime soon like Doc in “Back to the Future,” used cooking oil is a proven low-emissions feedstock for biofuels.
The oil used to cook your favorite crinkle-cut fries or fried chicken could be on a path to later fuel vehicles. But how does it get there?
Mendota Heights, Minnesota-based Restaurant Technologies is a cooking oil management company that collects used cooking oil from food service entities and takes it to one of 41 depots around the U.S.
It is one of the aggregators that supplies Chevron Renewable Energy Group (REG) with used cooking oil. The Ames, Iowa-based renewable fuels company then turns it into biodiesel or renewable diesel.
Getting used cooking oil from fryers to biofuel refineries
Restaurant Technologies supplies fresh cooking oil to food service entities such as restaurants, hotels, grocery stores and stadiums nationwide. An average quick-service restaurant, more commonly known as a fast food restaurant, has two 1,400-pound tanks of oil, each about the size of a water heater, Jeff Kiesel, CEO at Restaurant Technologies, told FreightWaves.
The company provides fresh oil and takes away used cooking oil using tanker trucks and a just-in-time delivery model. The tanks have sensors so Restaurant Technologies can see how much fresh oil is left and predict when it will need to switch out the oil.
The company’s oil tanker trucks get automatically routed to locations that need their oil switched out. An average quick-service restaurant needs its oil switched out every two weeks, Kiesel said. Larger manufacturers or casinos may need it daily.
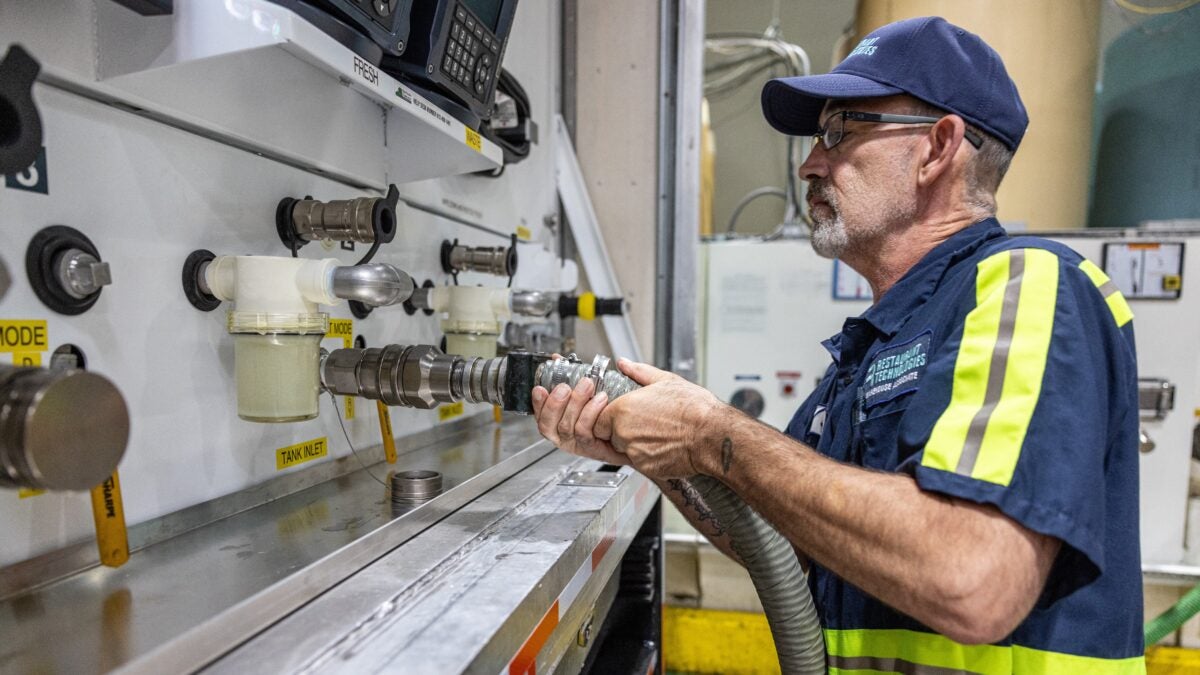
Hoses connect the truck’s oil tanks to the restaurant’s fryers and oil tanks. An automated system with a toggle switch allows workers to easily add, filter or dispose of cooking oil, Kiesel said.
“If people don’t use us, they’re doing that manually, which is carrying big 35-pound jugs of oil, pouring into the fryer, which is a mess, and then having hot oil carried outside and putting it into a dumpster. And then it gets picked up by a rendering company,” Kiesel said.
Dealing with cooking oil manually is a mess and a “very big safety issue” because it’s hot and can cause slips, Kiesel said. Rendering companies used to dispose of used cooking oil in landfills. Now some are recycling it for biofuels or other purposes.
The majority of oil is absorbed by the french fries, fried chicken or other happy hour-type foods cooked in it, Kiesel said. But what remains used to be difficult for restaurants to dispose of.
As fresh cooking oil leaves one of four fresh oil tanks on the sides of a Restaurant Technologies tanker truck, used cooking oil fills an empty tank in the center of the truck. Kiesel said this helps keep the truck balanced and combines delivery and collection of oil in one trip, making it more efficient.
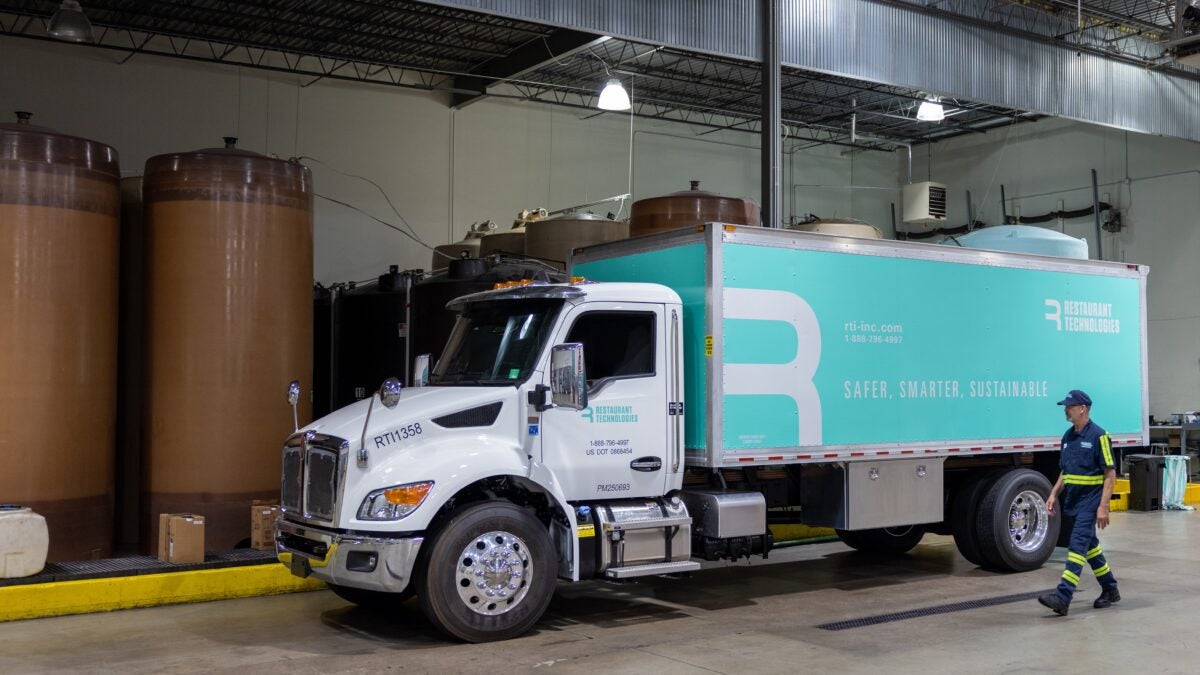
Once Restaurant Technologies delivers used cooking oil to one of its 41 depots, it filters the oil twice to remove any food particles. Keeping the oil in regulated tanks and tanker trucks throughout the entire process helps keep out excess moisture and contaminants.
REG contracts out tanker trucks to transport it to a refinery.
Restaurant Technologies has grown 12% annually over the past 15 years and now collects between 300 million pounds and 400 million pounds of used cooking oil each year, Kiesel said. About 75% of that goes to REG, and the rest goes to smaller local biofuel refineries.
Turning it into biodiesel, renewable diesel
Used cooking oil is one of 14 different types of feedstocks REG uses to produce biodiesel and renewable diesel.
“No matter what the feedstock is that we feed into our plants, we produce a quality biodiesel or renewable diesel that meets the common [American Society for Testing and Materials] specifications that most producers use,” Kevin Lucke, president at REG, told FreightWaves.
REG tests the used cooking oil it receives for quality control and then turns it into biodiesel or renewable diesel. The company produces biodiesel at its Midwest locations using alcohol and a catalyst. It produces renewable diesel at a plant in Louisiana by combining feedstocks with hydrogen and catalysts at a high temperature, Lucke said.
It would take about 8.5 pounds of used cooking oil to produce 1 gallon of biodiesel, according to Lucke.
Used cooking oil is always combined with other feedstocks, but the proportion of used cooking oil to other feedstocks used in a given day varies and depends on the cost of feedstocks. Lucke said it could make up between 5% and 20% of the feedstock mix in a day.
Does it smell like french fries?
People often wonder whether fuel made from used cooking oil smells like fried food when it’s used to power a vehicle. The short answer is no.
Used cooking oil is added into a mixture of several different feedstocks before being cleaned and processed into biodiesel or renewable diesel.
“We could use 100% used cooking oil, but for all practical purposes … they generally get mixed together,” Lucke said, noting that it certainly smells like french fries before processing but has no unusual odor afterward.
Kiesel said hobbyists sometimes try to run vehicles off of used cooking oil without processing it into a biodiesel or renewable diesel, and that would likely smell like french fries. But that’s not the case with renewable fuels that use used cooking oil as one of many feedstocks.
Read: Future-proofing diesel engines with renewable diesel — Net-Zero Carbon
Used cooking oil more expensive than fresh cooking oil
As the demand for biofuels such as biodiesel have increased drastically, “there’s much more demand for used cooking oil,” Lucke said. Adhering to basic economic principles, the cost of used cooking oil has also gone up.
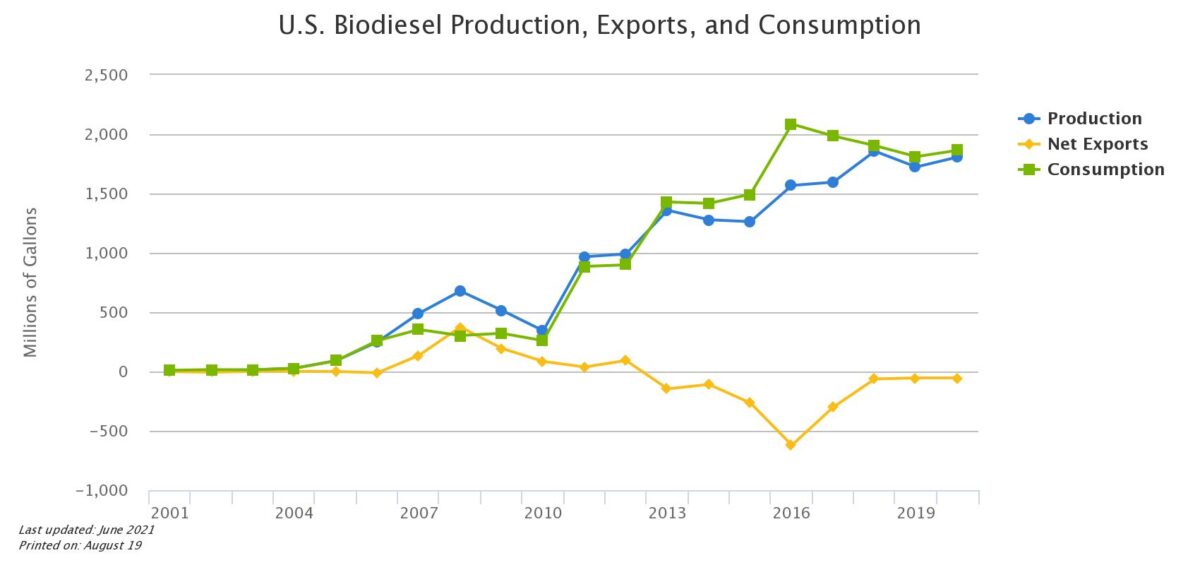
Whether purchasing used cooking oil for biofuels or animal products, “used cooking oil is actually worth more than fresh oil now because of the demand for green diesel and biodiesel,” Kiesel said.
Lucke said the cost of used cooking oil is quite volatile and follows the energy and soybean market.
Restaurants used to have to pay rendering companies to dispose of their used cooking oil the way companies pay for waste collection. But that has changed since used cooking oil is now a valuable input for products such as biodiesel.
“Anybody who collects used cooking oil sells it to the highest bidder for all different uses,” Kiesel said. Since the demand for biofuels is higher than the supply, “all those other uses are going to have to really pay up to get access to the used cooking oil.”
He said most, if not all, cooking oil is recycled in some way after it’s used for cooking. So it’s being taken from other potential uses such as animal feed or chemicals to make biofuels.
But the best environmental impact would be to use it for renewable fuel, Kiesel said. “No doubt about it.”
Emissions impacts of biodiesel and renewable diesel
Used cooking oil has the lowest carbon footprint of all biofuel feedstocks, including soybeans, corn or canola oil, Kiesel said.
According to a 2022 Argonne National Laboratory study, petroleum diesel resulted in 90 grams of carbon dioxide equivalent emissions per megajoule of energy. That number was only 15 for biodiesel and renewable diesel produced from used cooking oil, an approximately 83% reduction.
That means fuels produced from used cooking oil have a much lower carbon intensity; they can provide the same amount of energy to a vehicle with much lower carbon emissions.
But biodiesel and renewable diesel are produced using several feedstocks, so the carbon emissions vary depending on the mix of feedstocks and the blend levels of biodiesel.
According to the Department of Energy, 100% biodiesel, or B100, can lower GHG emissions by 74% compared to conventional diesel. Lower blends of biodiesel such as B20, 20% biodiesel and 80% conventional diesel, have a lower reduction in GHG emissions than B100.
One drawback with biodiesel is the higher the blend is, the more nitrous oxides it emits. NOx emissions are air pollutants that harm human health.
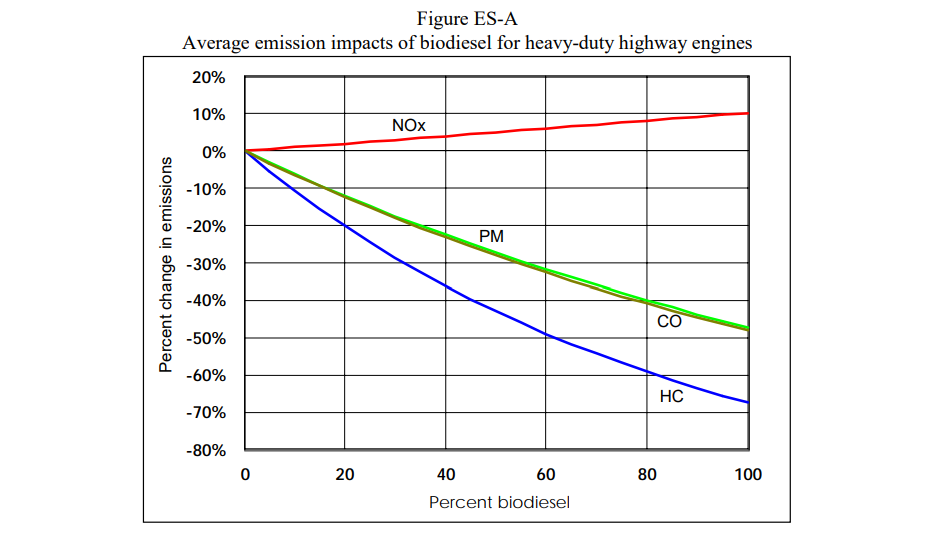
Biodiesel has weather, blending limitations
Widely accepted biodiesel blends have risen from B5 to B10 and B20. That increase in biodiesel approved is related to more sophisticated processes for collecting and cleaning used cooking oil and advancements in the biodiesel production process, Lucke said.
B20 is the highest blend of biodiesel that most OEMs have approved for heavy-duty vehicles, but Lucke said REG is “actively working with OEMs on higher blend acceptance.”
Cold weather is still an issue for biodiesel. It has a higher freezing point than conventional diesel, so fleets generally can’t fuel up with high biodiesel blends in winter.
“You will very rarely see anything above 20% biodiesel blends in in the wintertime,” Lucke said.
Drivers can use 100% renewable diesel without any issues in cold weather. However, renewable diesel plants are much more expensive to build, and the fuel is newer and less readily available right now.
Read: Renewable diesel: Environmental and economic sustainability meet head-on
REG recently introduced UltraClean fuels, which are blends of biodiesel and renewable diesel.
Ultraclean is “a combination of both biodiesel and renewable diesel, and it actually is a good combination. Both of those products together provide the benefits that our customers are looking for,” Lucke said.
UltraClean fuels can reduce emissions of particulate matter, a known air pollutant, by more than 45% and reduce carbon emissions by up to 40%, according to REG.
Closing the loop
Restaurant Technologies is planning a pilot project in Des Moines, Iowa. The used cooking oil the company collects and supplies to REG will be turned into biodiesel and then used to fuel Restaurant Technologies’ trucks that deliver and pick up cooking oil.
“We’ll be closed-looping from our depots, going right to REG’s facility and then we’ll be filling up our trucks with biodiesel made from our own used cooking oil,” Kiesel said.
The company is looking at expanding this type of project to other cities it operates in as well.
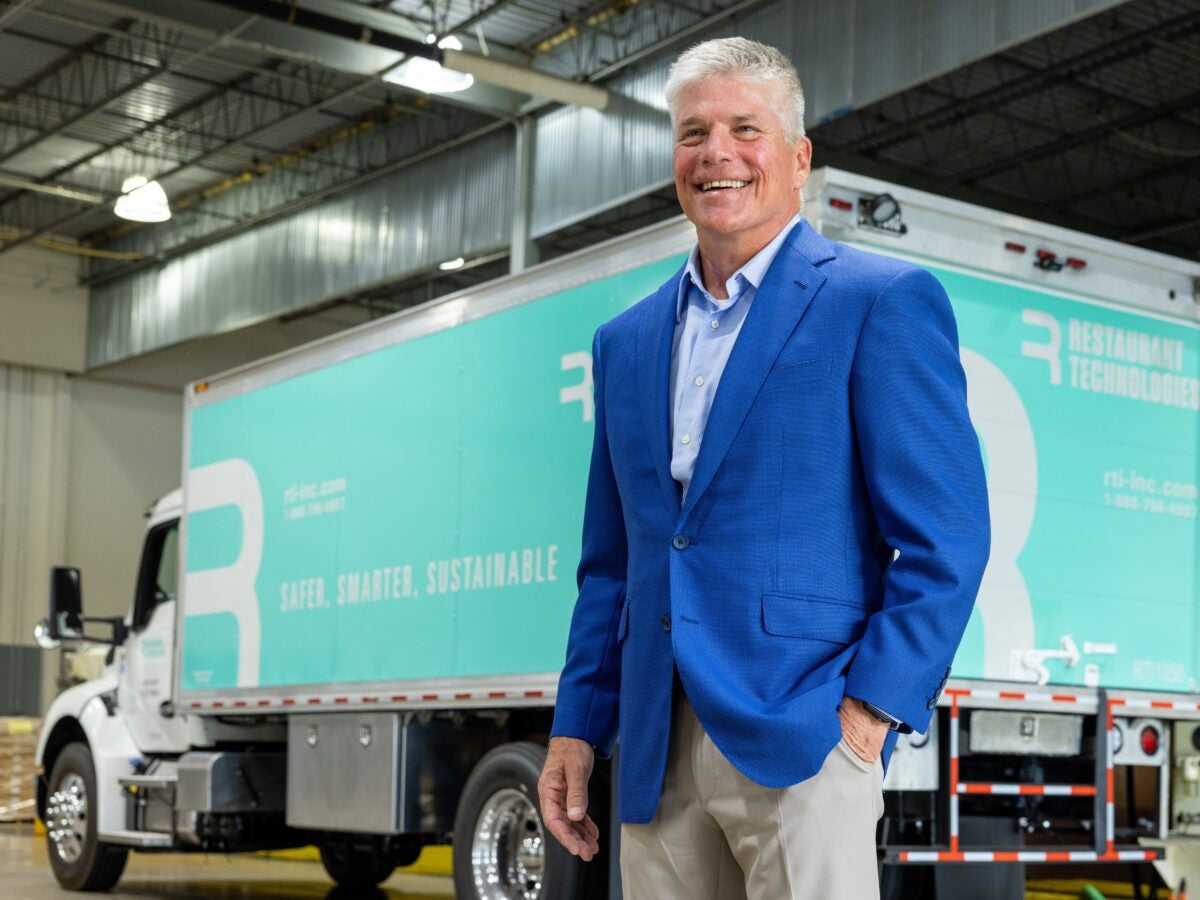
Some of Restaurant Technologies’ larger customers such as Shake Shack know their used cooking oil is being recycled and turned into fuel. “We’re part of their [environmental, social and governance] story,” Kiesel said.
He said customers will likely start to educate their customers about the sustainability impacts of what Restaurant Technologies is doing in partnership with REG.
Lucke added, “Chevron has very high growth ambitions of having the capacity to produce 100,000 barrels a day of renewable fuels. Chevron REG will play a big role in that. REG has been in this business for a long time and is one of the biofuels leaders in this space.”
Click here for more FreightWaves articles by Alyssa Sporrer.
Related Stories:
Texas researchers’ new breed of peanuts may boost biodiesel production
Study: Biodiesel packs major health and economic benefits
This company wants to turn your trash into biofuel and other useful stuff
Trucking industry concerned about SEC’s proposed climate rules